

Among the advantages of the rotational mold we find:
- Design Versatility: This process allows the creation of shapes of various thicknesses by co-moulding metal inserts without the need of assembling multiple components.
- Reduced Production Costs: Compared to other processes, rotational molding can be more cost-effective for producing large parts or parts with particular shapes.
- Waste reduction: Because the plastic material is evenly distributed within the module, there is less material waste than with other manufacturing processes.
- Flexible production: It can be used to produce both small batches and large volumes of parts.
- Reduced investment in equipment: The molds necessary for rotational molding production have a lower economic impact than other plastics technologies.
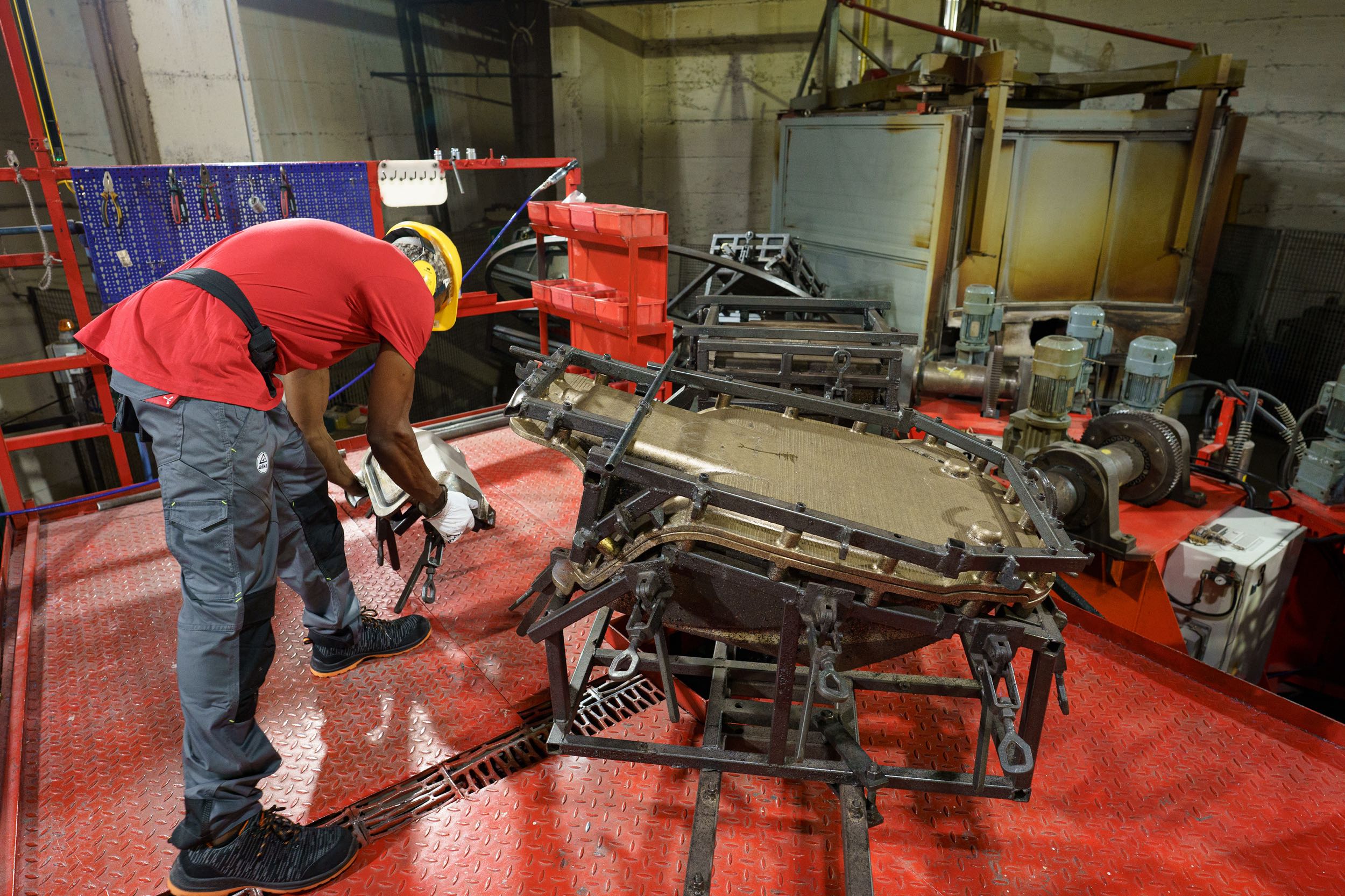
Among the advantages of the rotational mold we find:
- Design Versatility: This process allows the creation of shapes of various thicknesses by co-moulding metal inserts without the need of assembling multiple components.
- Reduced Production Costs: Compared to other processes, rotational molding can be more cost-effective for producing large parts or parts with particular shapes.
- Waste reduction: Because the plastic material is evenly distributed within the module, there is less material waste than with other manufacturing processes.
- Flexible production: It can be used to produce both small batches and large volumes of parts.
- Reduced investment in equipment: The molds necessary for rotational molding production have a lower economic impact than other plastics technologies.
HOW IT WORKS:
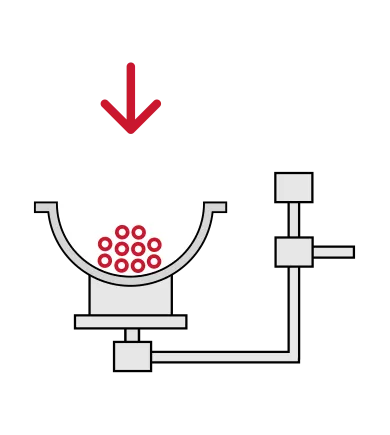
The micronized powder raw material, previously dosed, is introduced into a mould, specially made of steel or aluminium, which It is installed on a rotational machine arm.
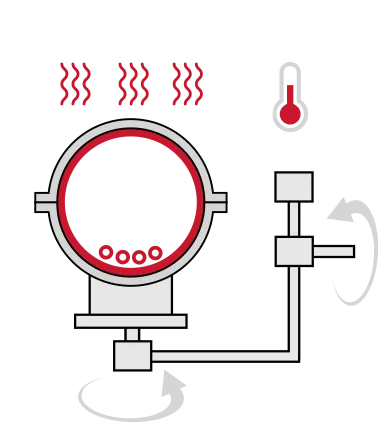
By rotating on two axes, the mould enters the dedicated oven where the heat melts the raw material that becomes liquid and viscous and that thanks to the movement of the rotational, adheres evenly to the module walls.
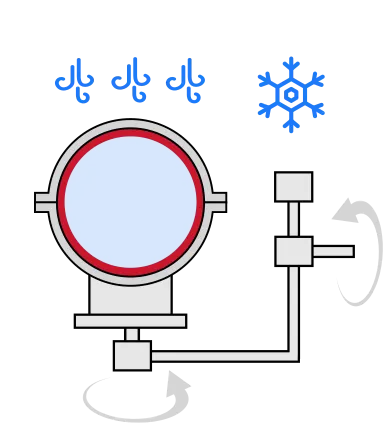
With a control system that coordinates all phases of the process, ensuring certain times, we move on to the air cooling phase, maintaining the mould in rotation and offering the best quality standards for the resistance of the product and homogeneity.
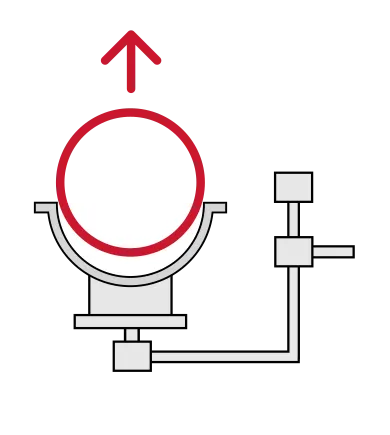
Once the process is complete, the components of the mould are opened and the artifact is extracted to be sent to the subsequent control phases quality, customization and testing to be then sent to the customer.
Rotomoulded part is a seamless plastic product that can be made of different materials such as polyethylene, polyamide, polypropylene.; even in multilayer with 2 or more layers of polyethylene (PE), in a single implementation cycle with the possibility of co-molding FOAM PE thus obtaining insulated products thermally and/or acoustically.
Through the molds, it is possible to replicate any type of texture and roughness on all hollow bodies produced; In addition, it is also possible to obtain a mirror polishing directly into the module, or through flame (flaming) in the finishing process.
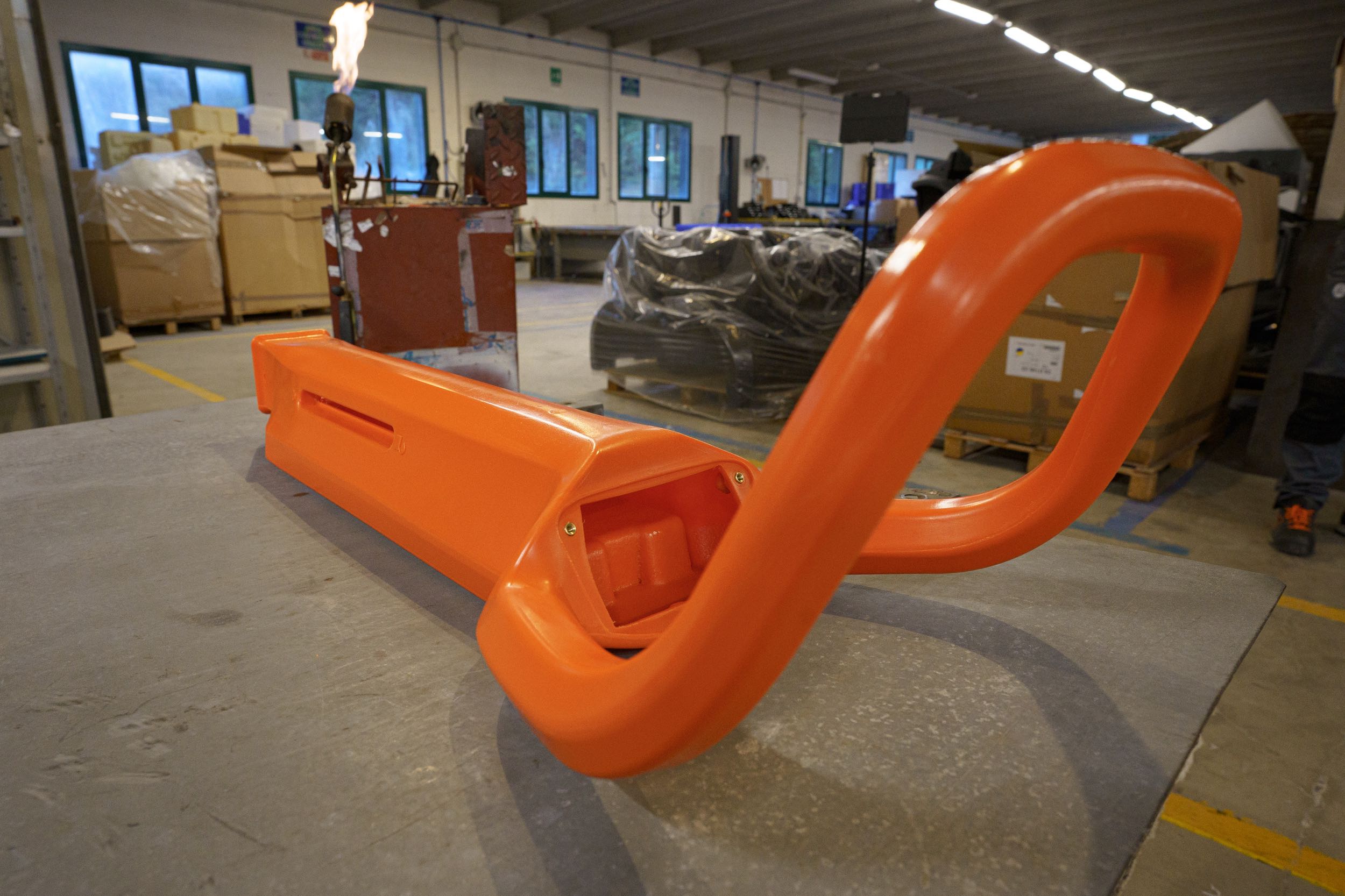
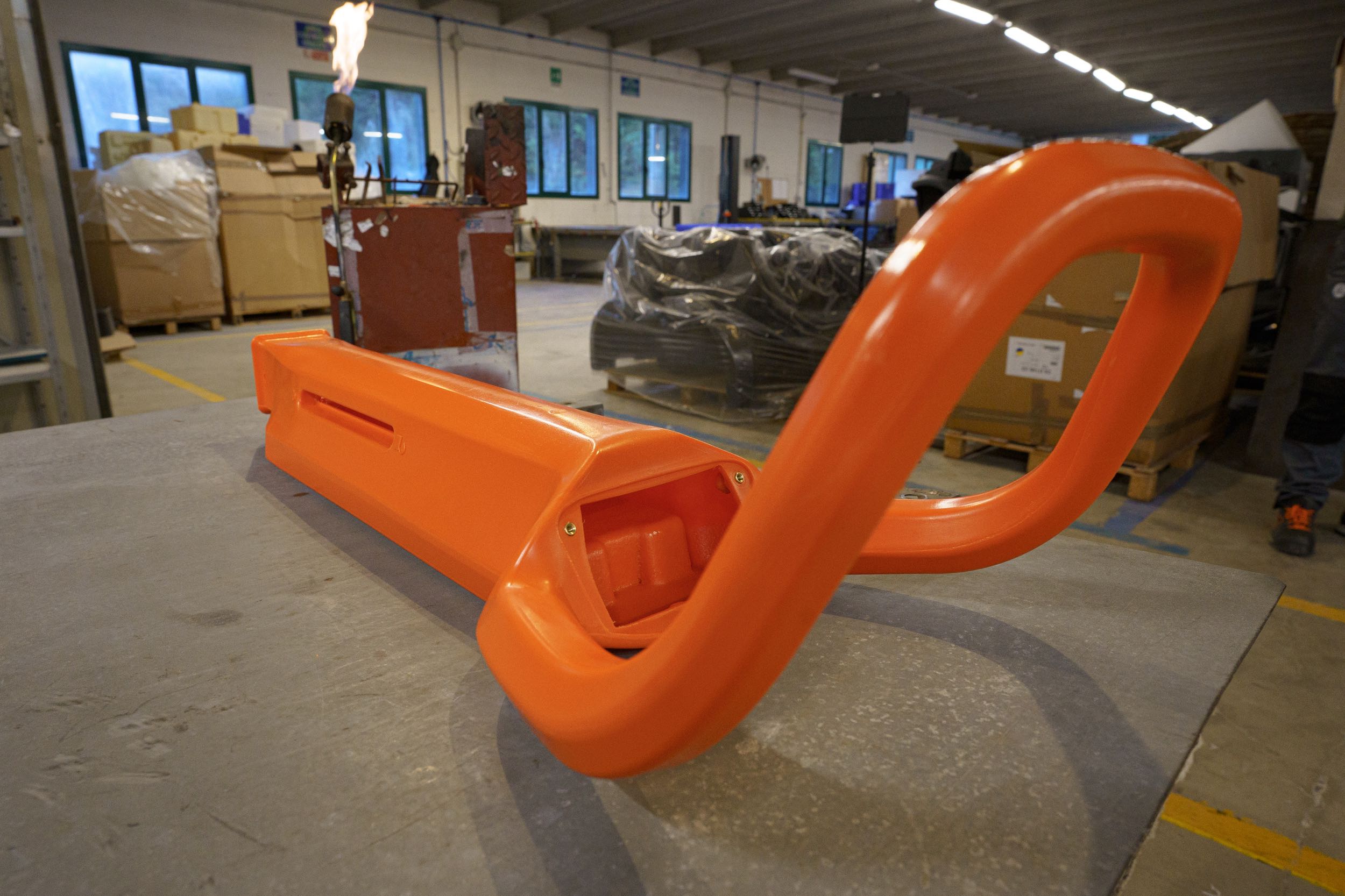
Rotoformed tiles do not require painting, as they can be made in any color thanks to the mass pigmentation of the raw material, obtaining any RAL or pantone.
Depending on the design requirements, it is possible to produce hollow monoliths enriched with various types of metal elements, such as flanges and threaded inserts (metric or gas), high-quality screen printing and labels; These additional parts merge completely with the hollow part, as they are integrated synergistically during the moulding process.
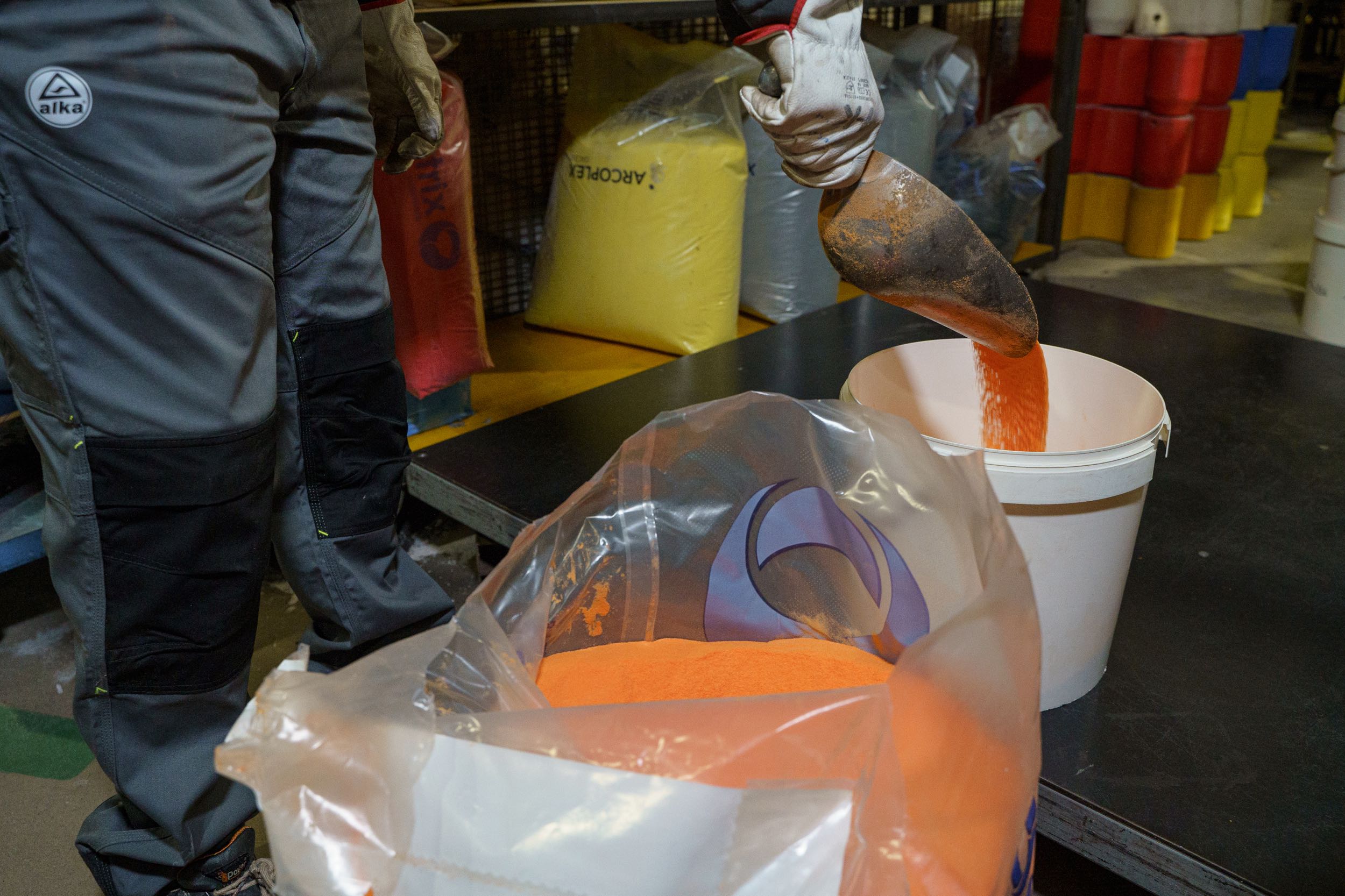
Rotoformed tiles do not require painting, as they can be made in any color thanks to the mass pigmentation of the raw material, obtaining any RAL or pantone.
Depending on the design requirements, it is possible to produce hollow monoliths enriched with various types of metal elements, such as flanges and threaded inserts (metric or gas), high-quality screen printing and labels; These additional parts merge completely with the hollow part, as they are integrated synergistically during the moulding process.
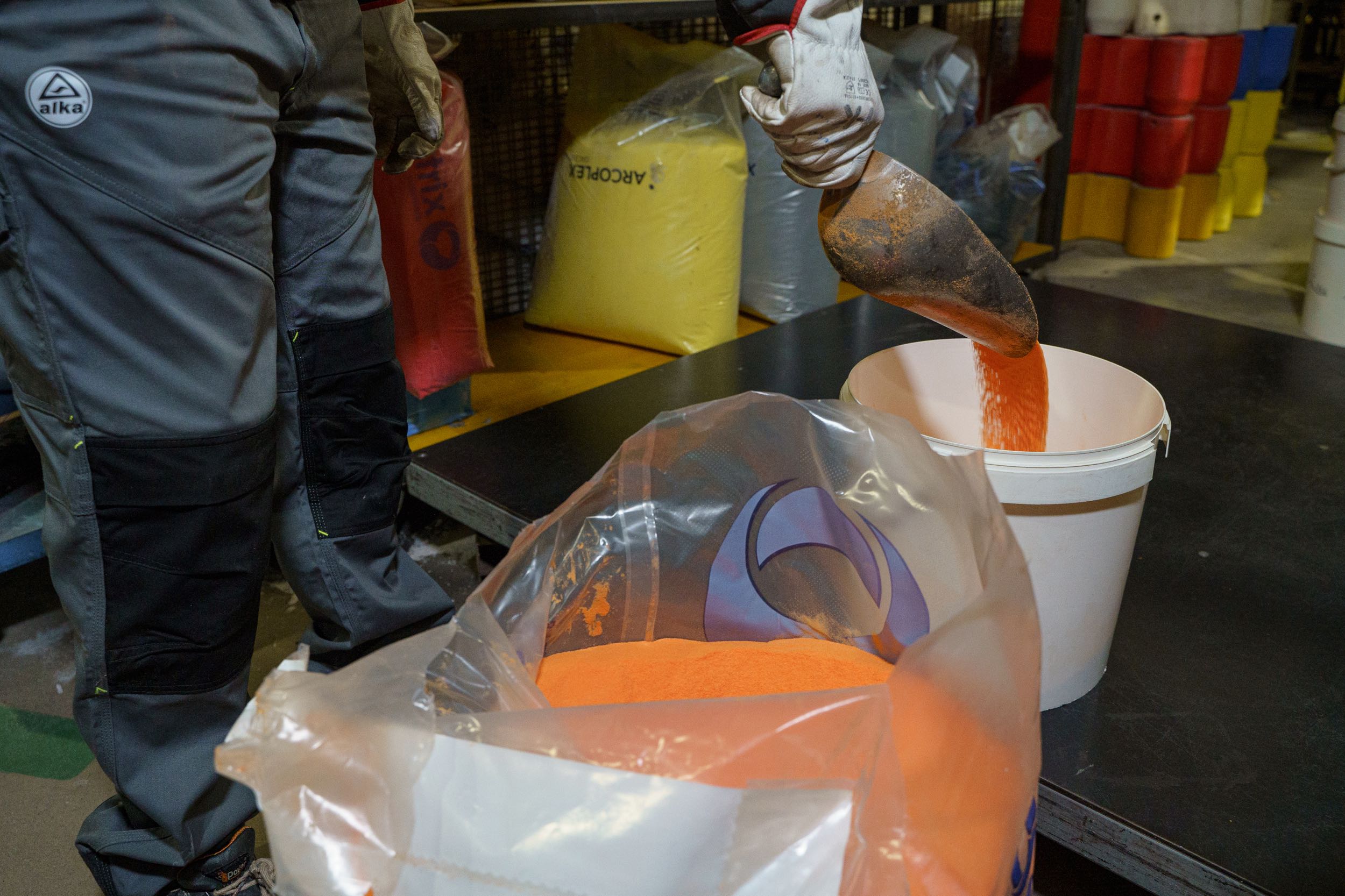
Rotoformed tiles do not require painting, as they can be made in any color thanks to the mass pigmentation of the raw material, obtaining any RAL or pantone.
Depending on the design requirements, it is possible to produce hollow monoliths enriched with various types of metal elements, such as flanges and threaded inserts (metric or gas), high-quality screen printing and labels; These additional parts merge completely with the hollow part, as they are integrated synergistically during the moulding process.