

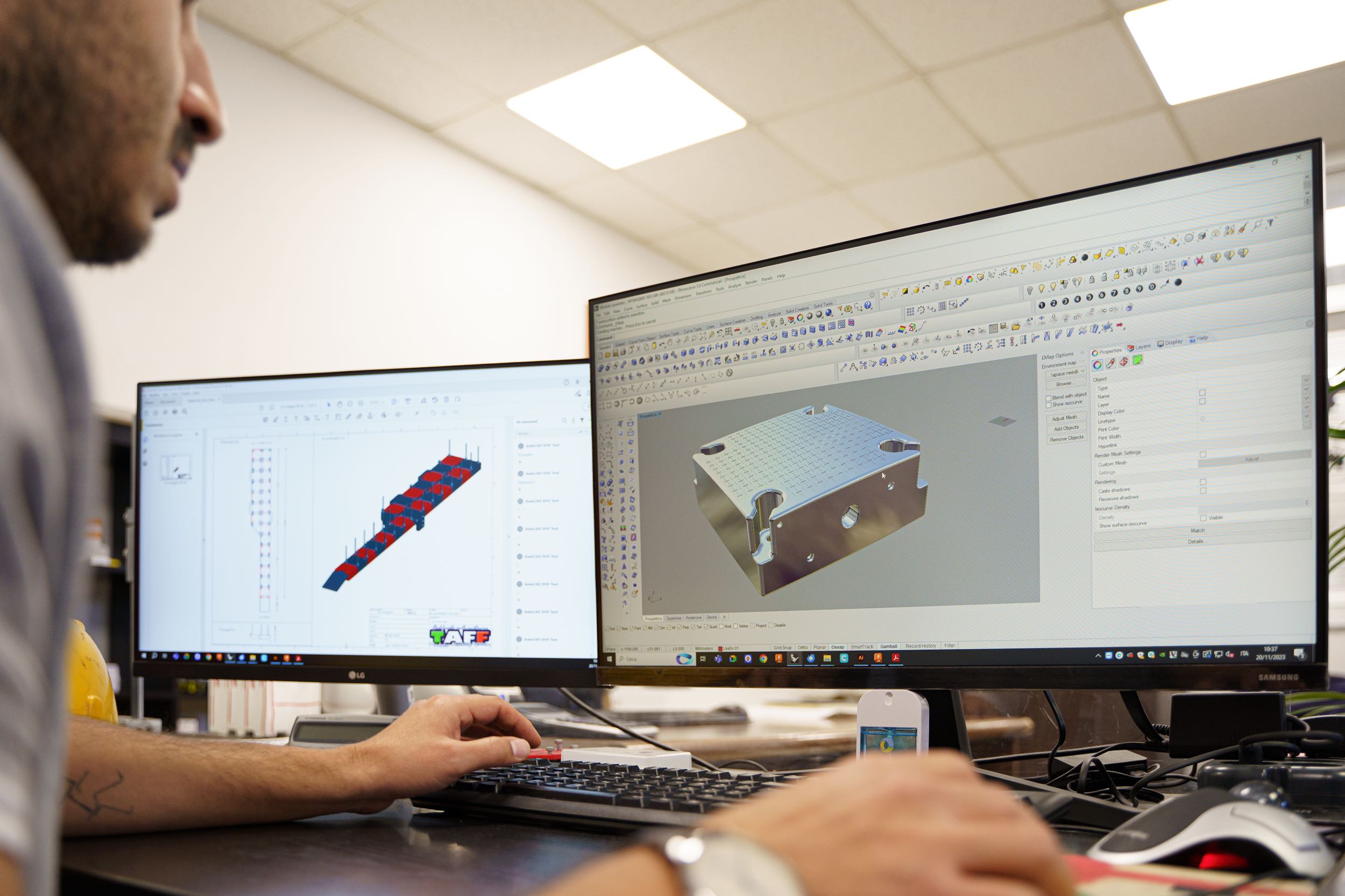
DESIGN
We use a three-dimensional modeler for the realization of projects from scratch, or to integrate those already provided by the customer; we associate a second software to perform preventive tests on the project, being able to identify any critical issues before its serial creation.
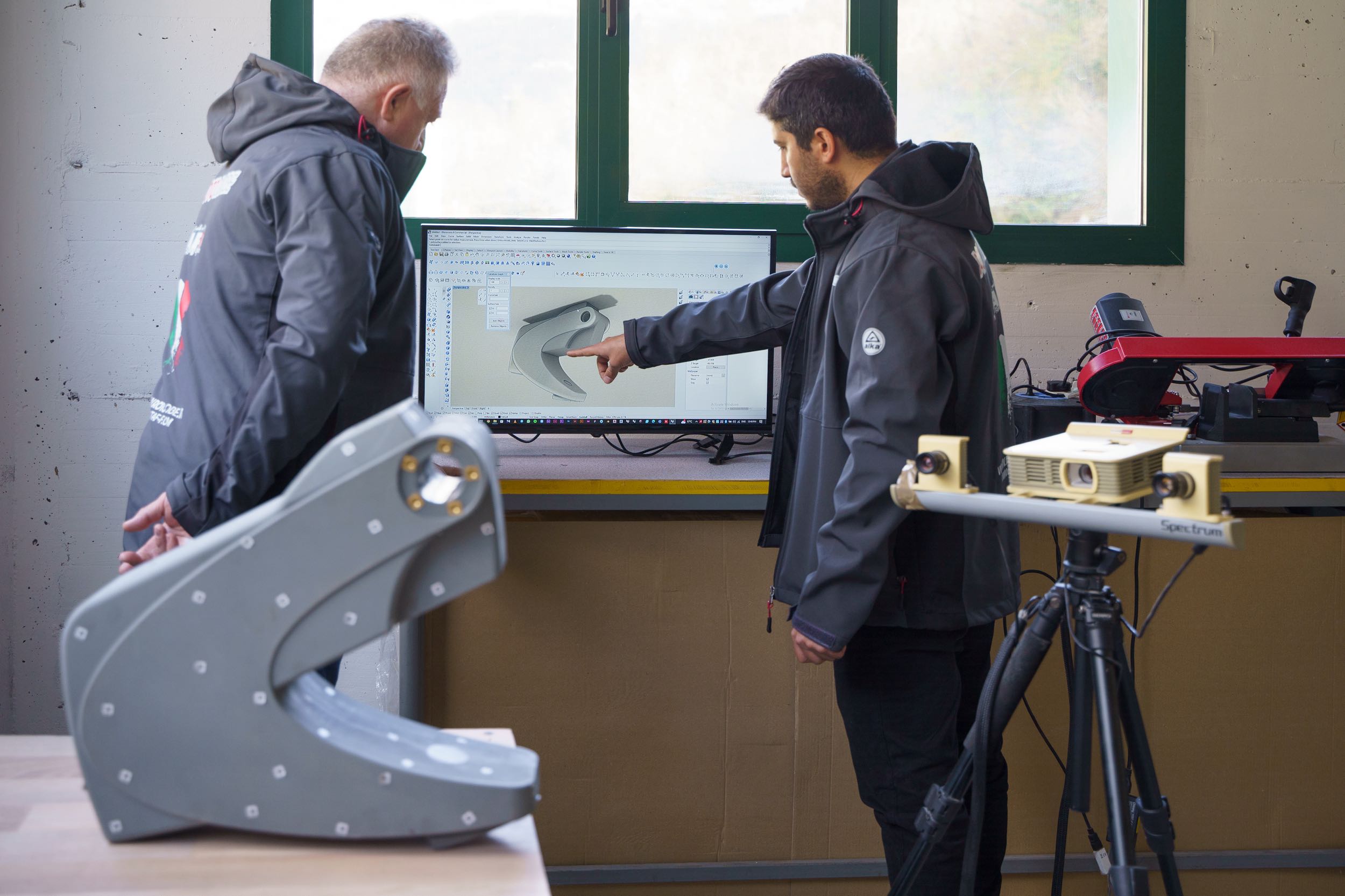
In this phase we carry out studies on the raw materials to be used, with the best mechanical characteristics for the desired customization and we create prototypes and three-dimensional models thanks to 3D printers and scanners, guaranteeing the best consulting solutions.
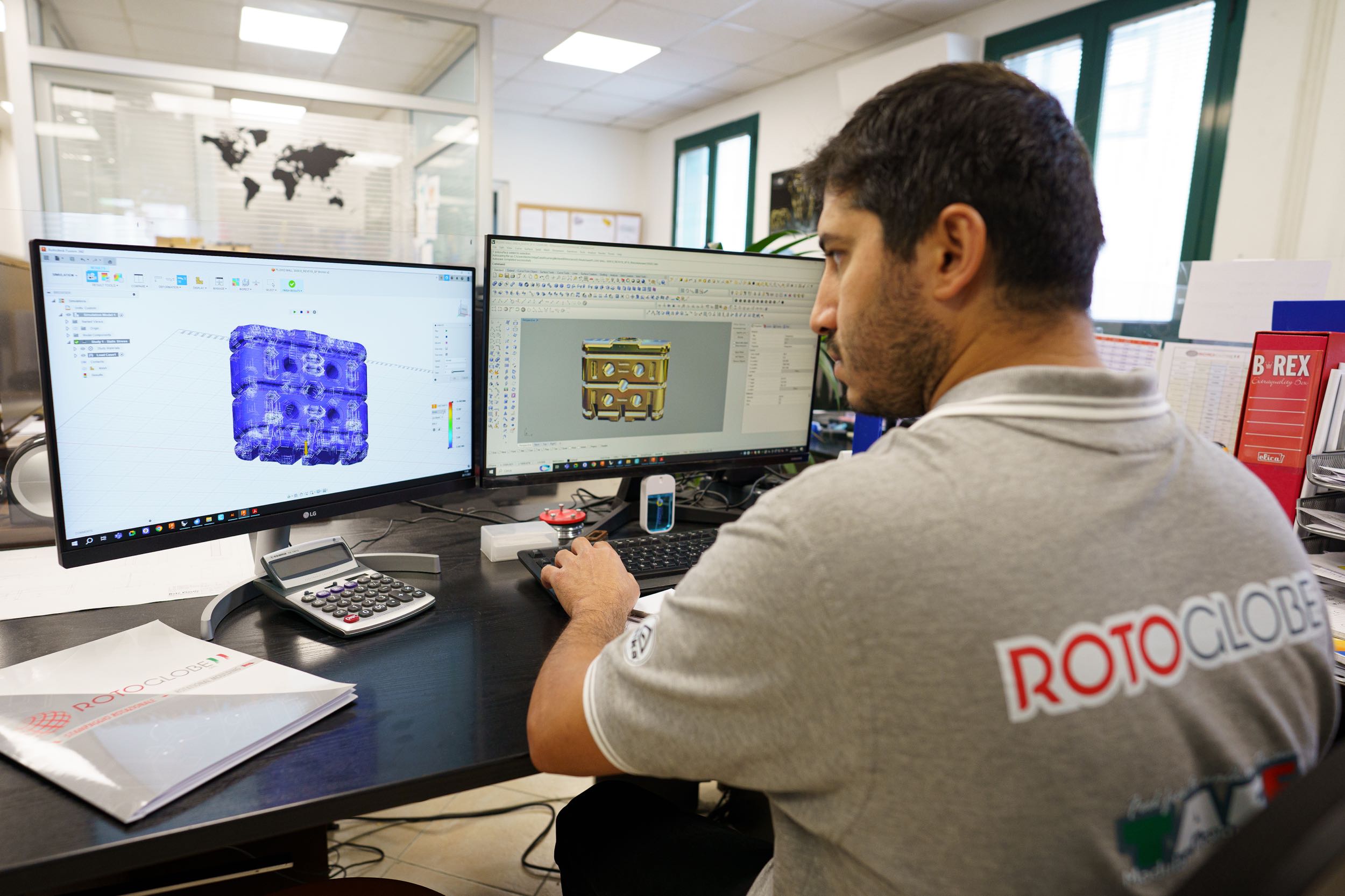
Once all the design aspects have been defined, we create and enter a technical bill of materials to ERP to ensure that every detail is followed and respected.
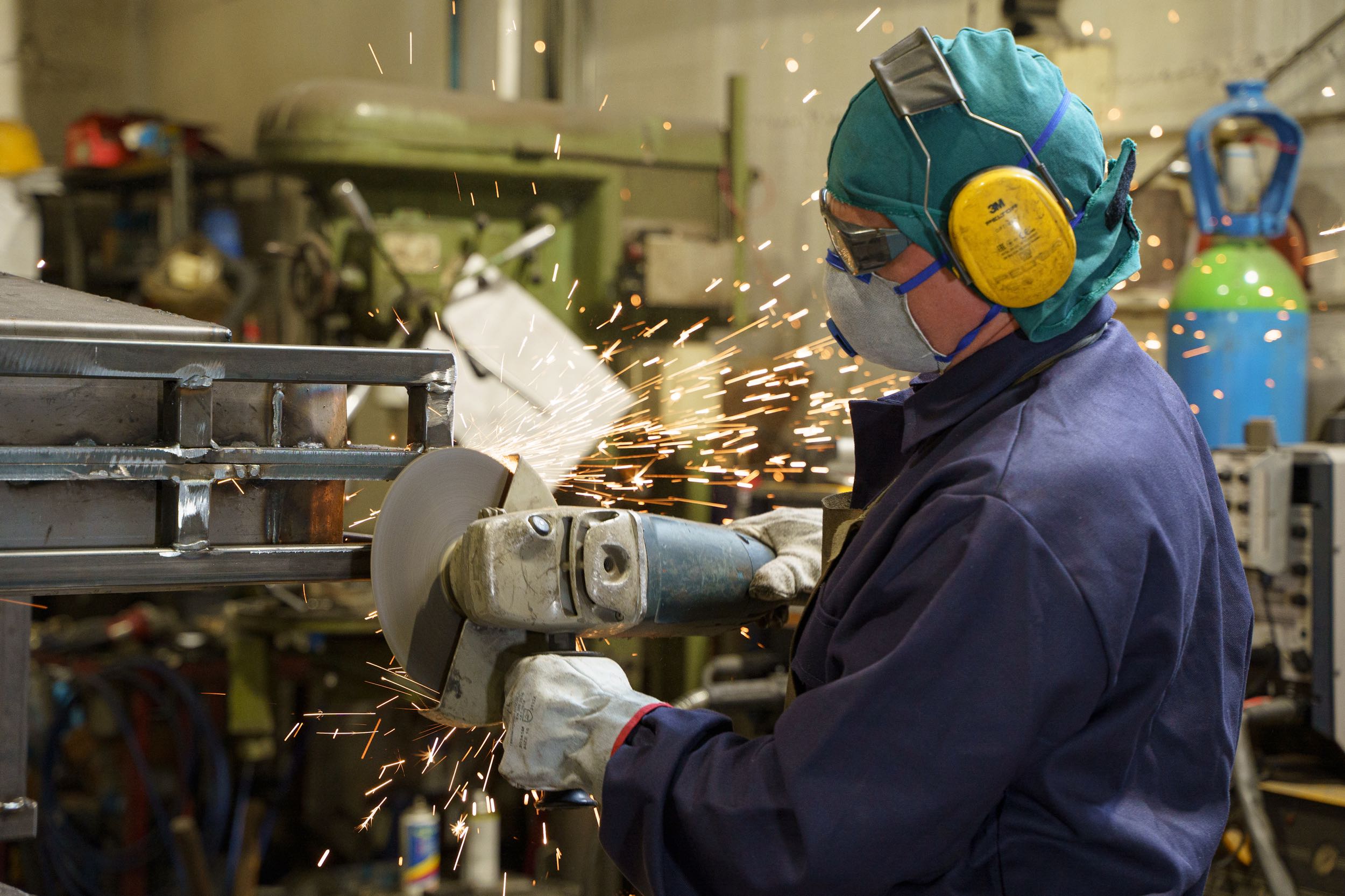
MOLD CREATION
Based on the design needs, we can offer steel moulds (produced directly in Rotoglobe’s internal workshop), or cast aluminium or CNC milled modules of solid aluminium block through first level external partners.
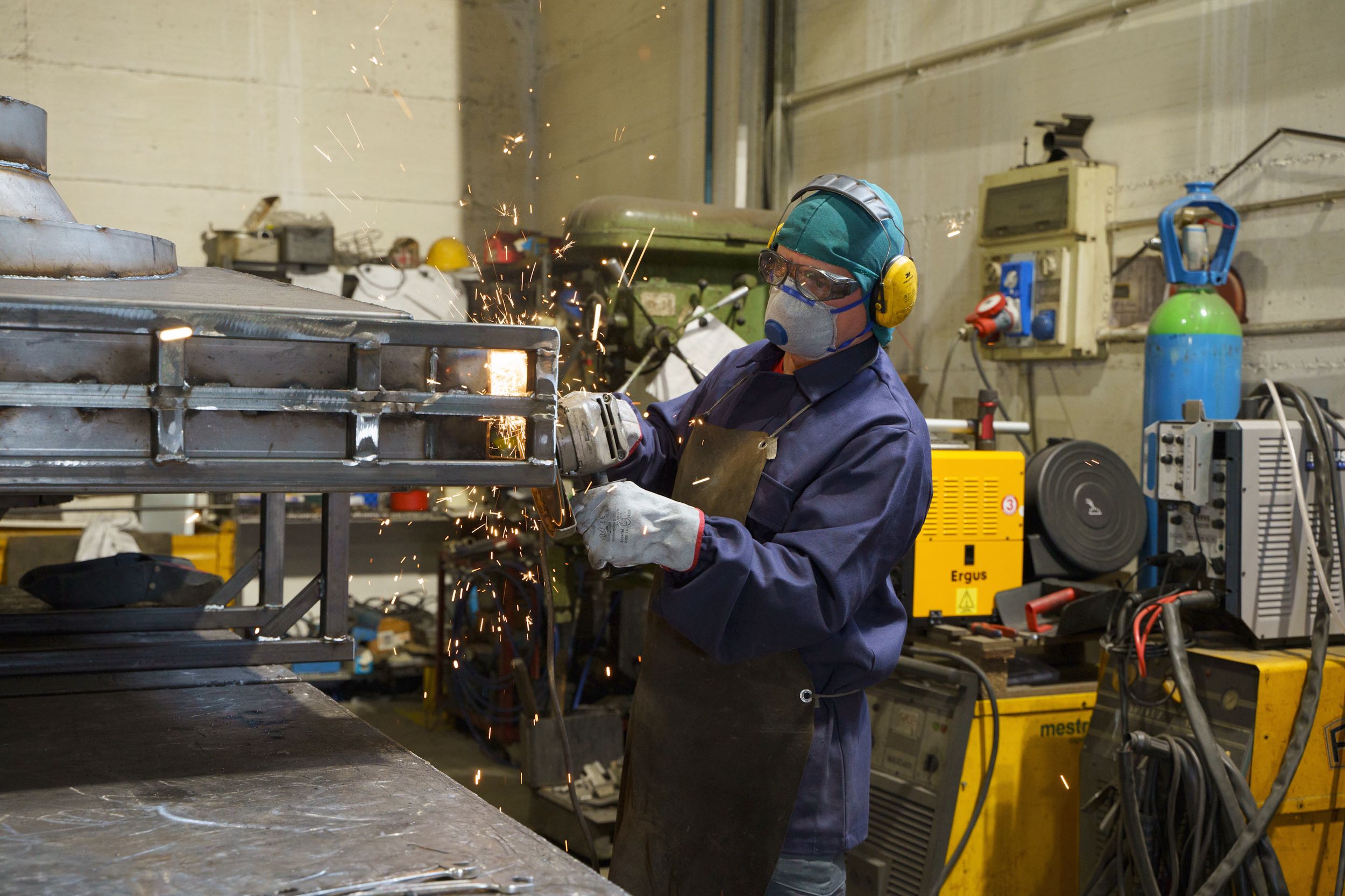
The presence of a fully equipped mechanical workshop allows, not only to make molds, but to intervene quickly on maintenance and repairs, without affecting the production rate and delivery times of the products.
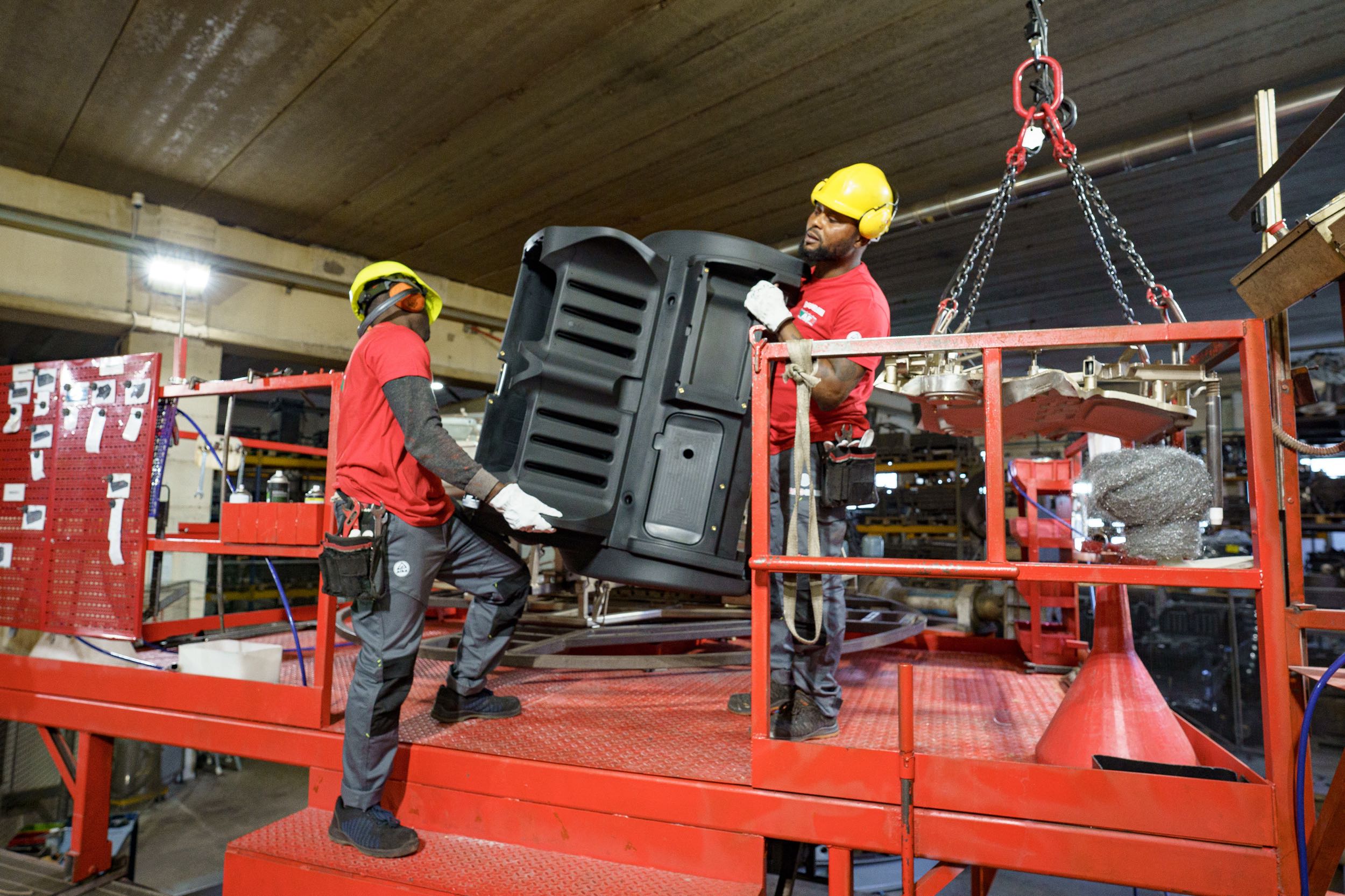
ARTIFACT PRODUCTION
The raw material, such as 100% virgin polyethylene powder, is inserted inside a mold which, placed on a “mechanical arm” is rotated on two axes.
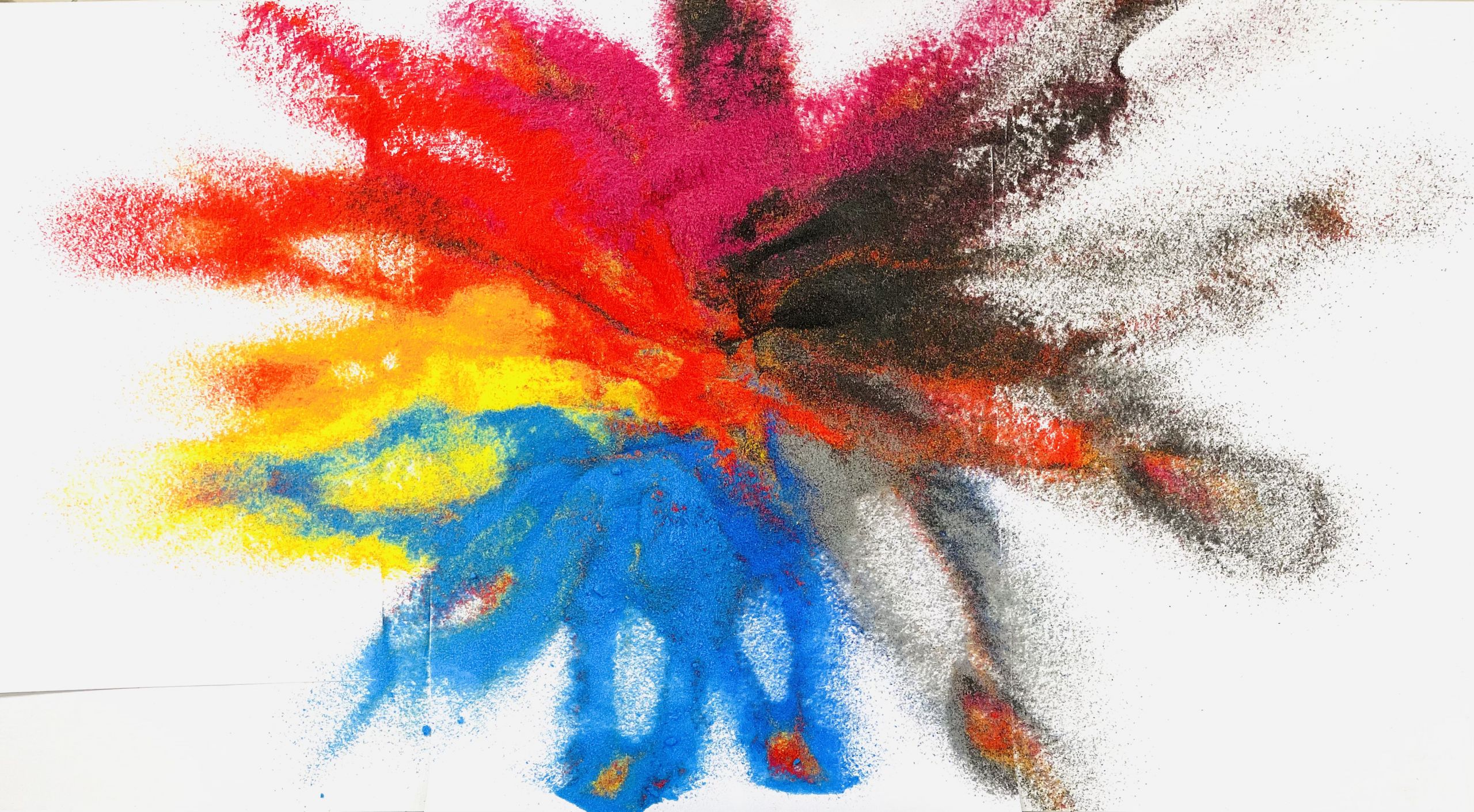
With the supervision of a single control system, safety and compliance with times and temperatures are guaranteed to provide the best result. Small and large products of different sizes, different layers and plastic materials such as polyethylene, HDPE, MDPE, LDPE, polyamide, polypropylene can be realized. At the end of the printing process, the part is examined and identified with a unique serial number, which allows the traceability of the product throughout the subsequent phases.
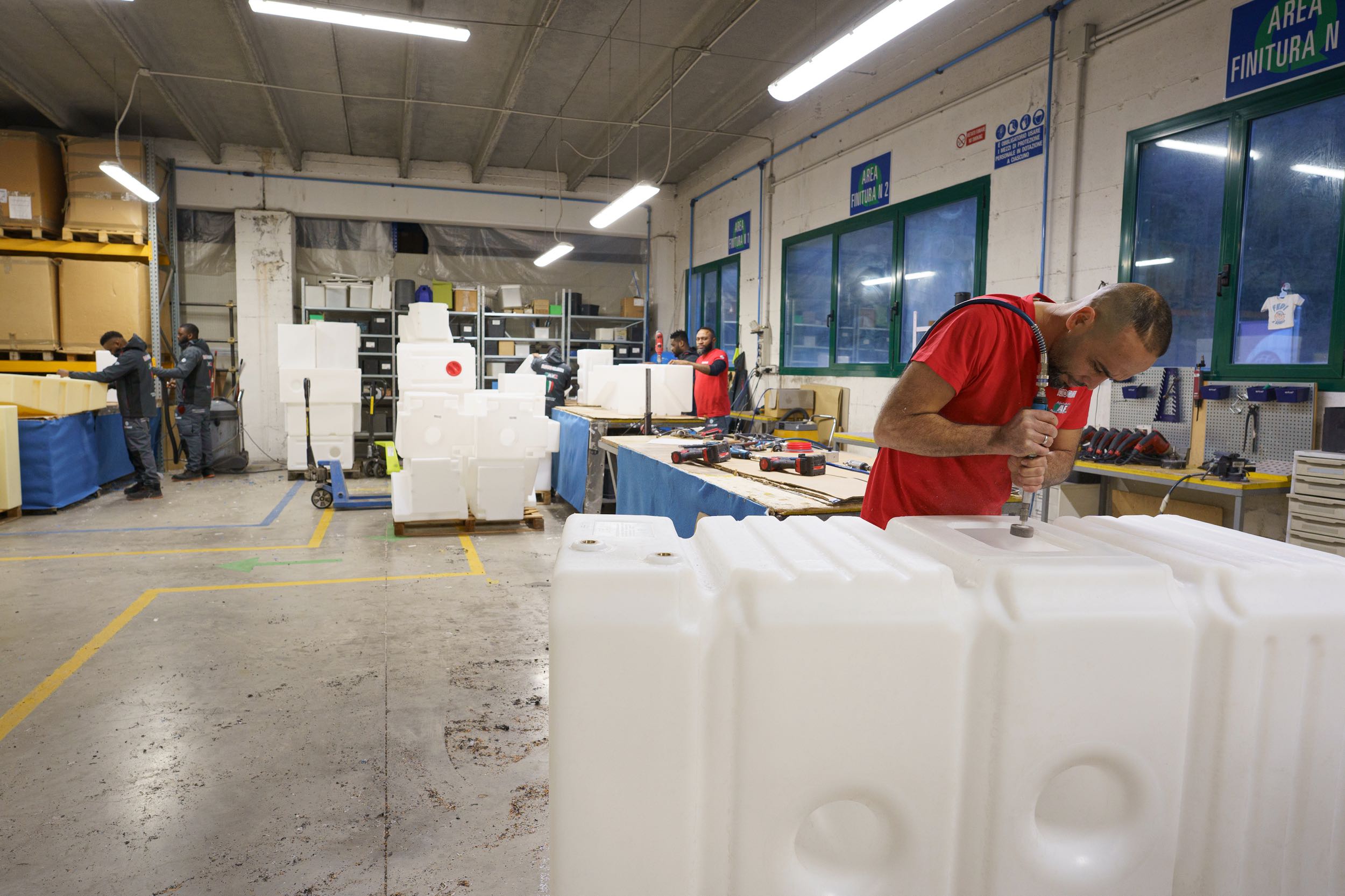
FINISHING
Where a dedicated team equipped with all standard assembly equipment and electric and pneumatic drills, manual and stationary cutters, deburrers, threading machines, tappers, finishes and completes the hollow thermoformed with the assembly of all the necessary accessories, and all the technical and aesthetic processes listed above are carried out based on the original project.
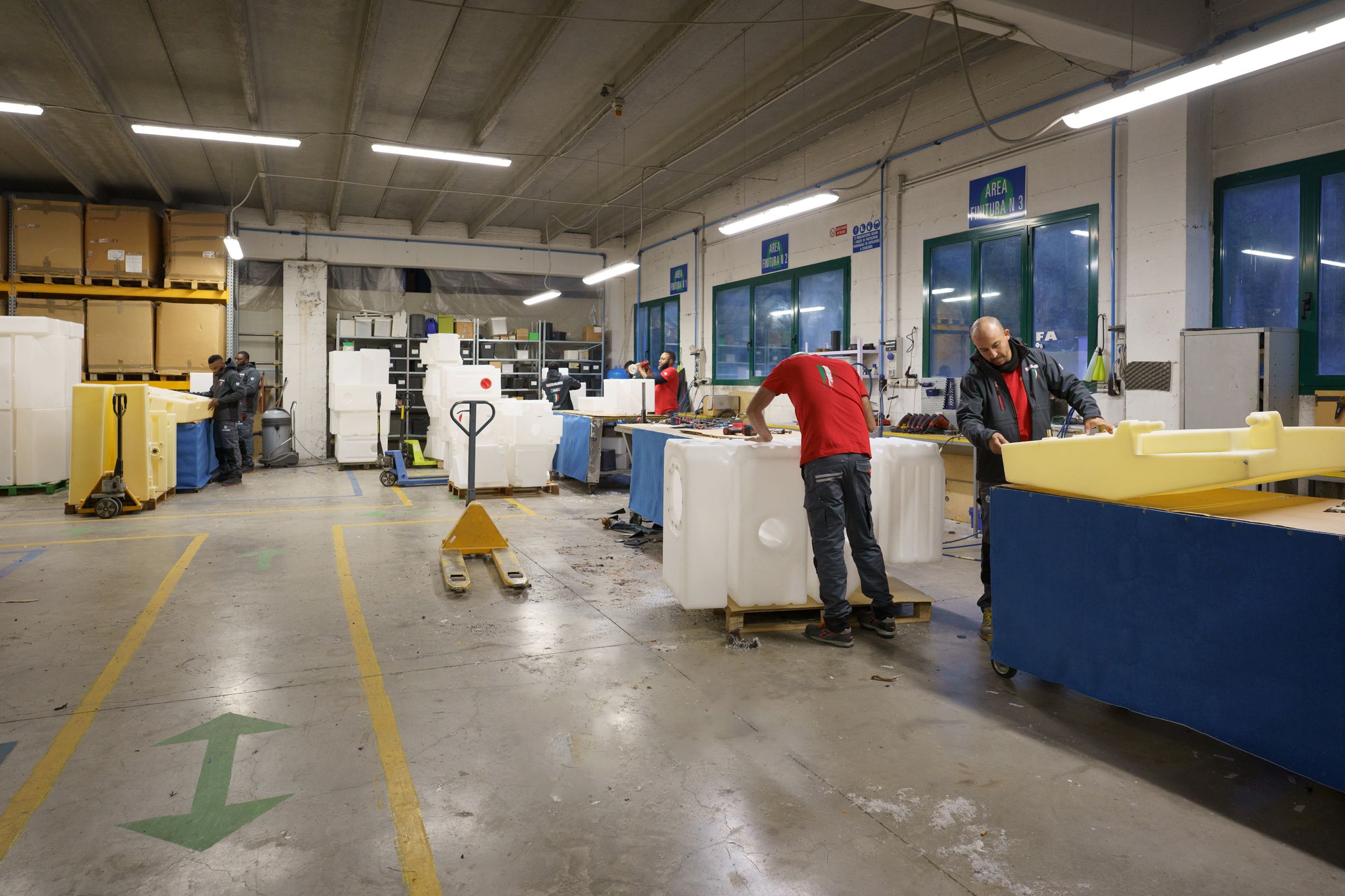
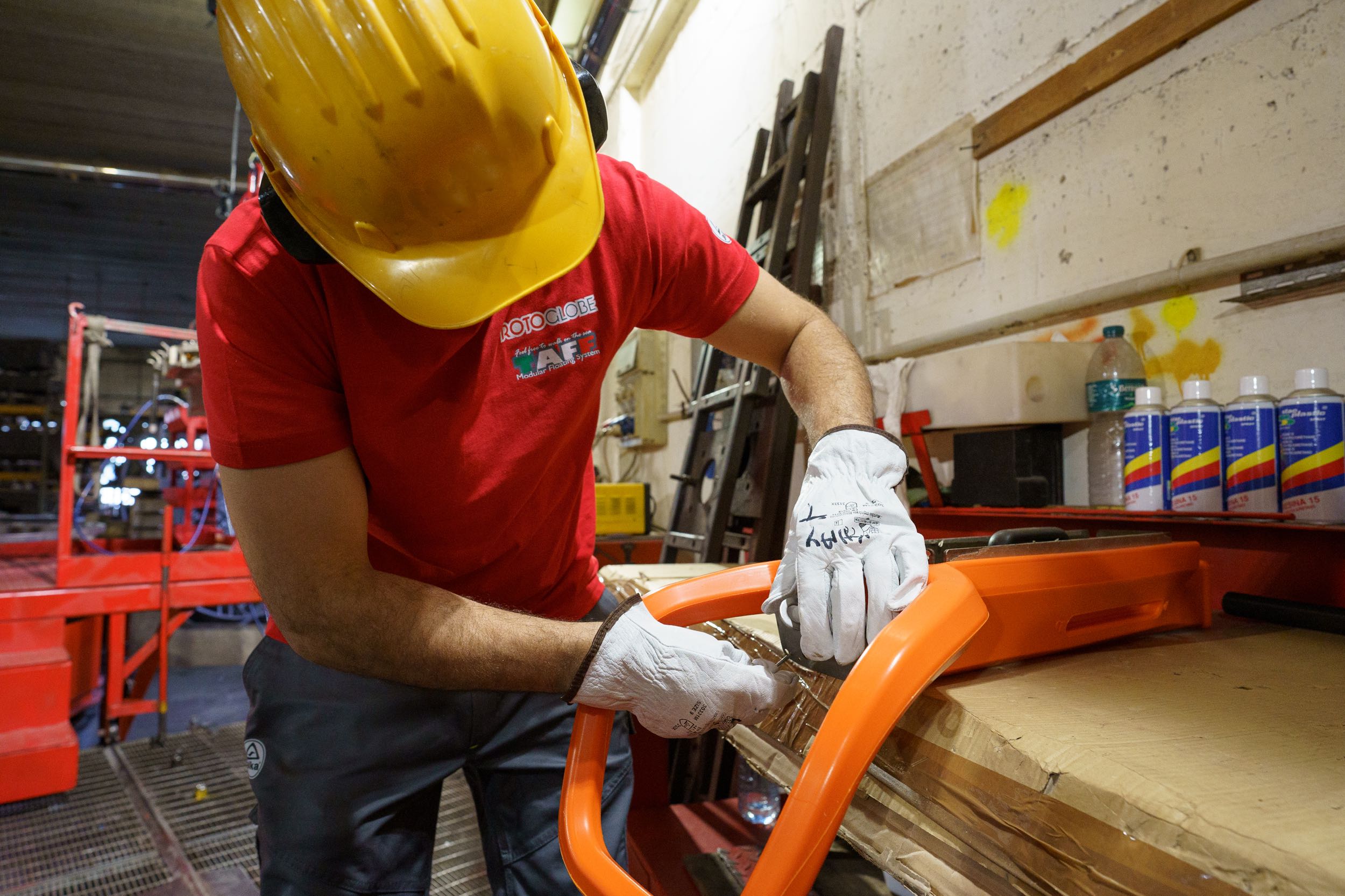
TEST
The test includes 100% coverage of the production for the pneumatic leak test, a coverage of 10% of production for cyclic testing in addition to customer satisfaction Customized testing requests agreed with the customer. This phase concludes By showing a special “Test OK” label on the product.
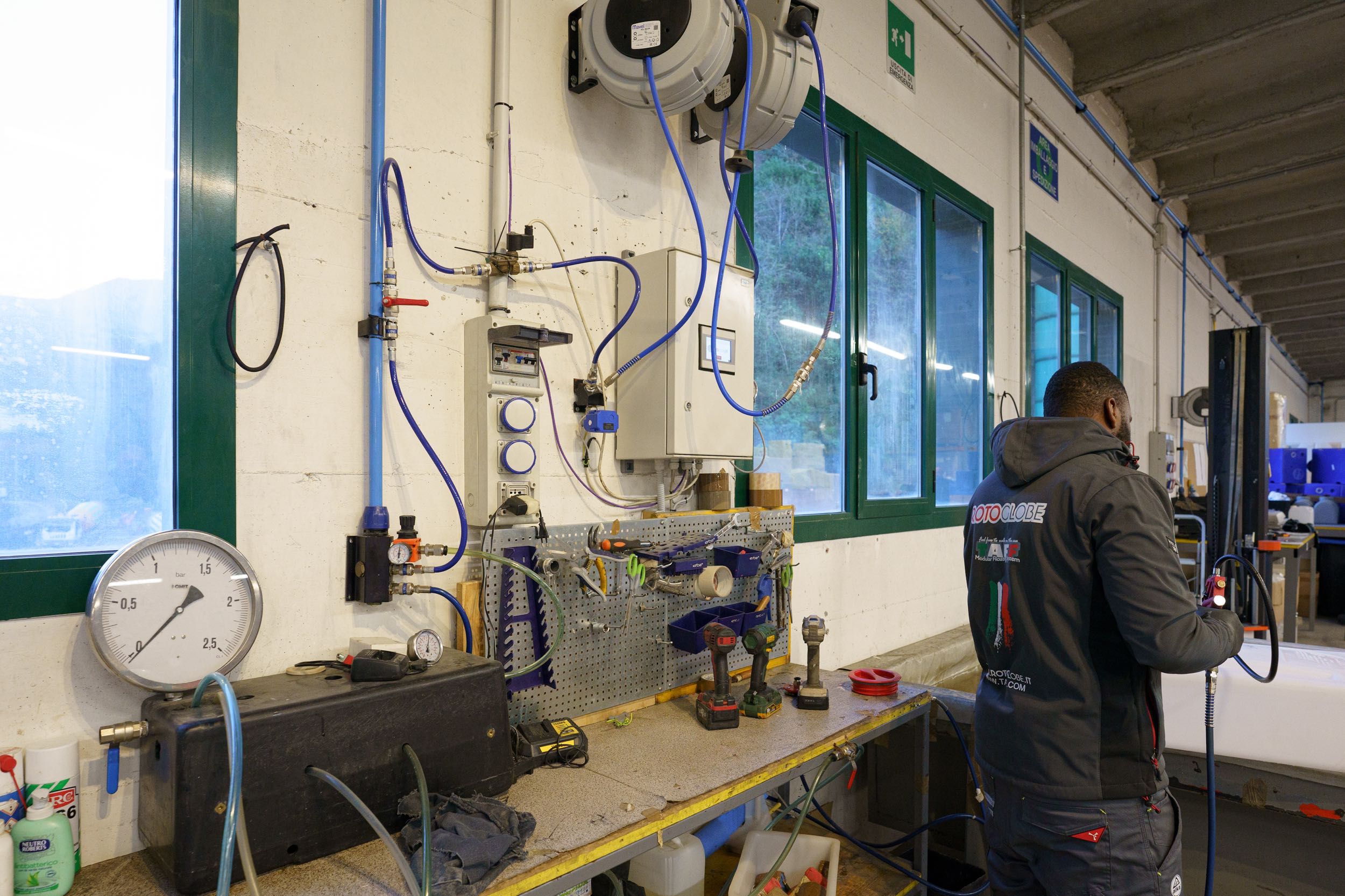
In the testing area there is also a controlled pneumatic station for the verification of the integrity of the tanks, a station for the creation of the certificate of CE examination of the product and a 3D scanner for dimensional checks.
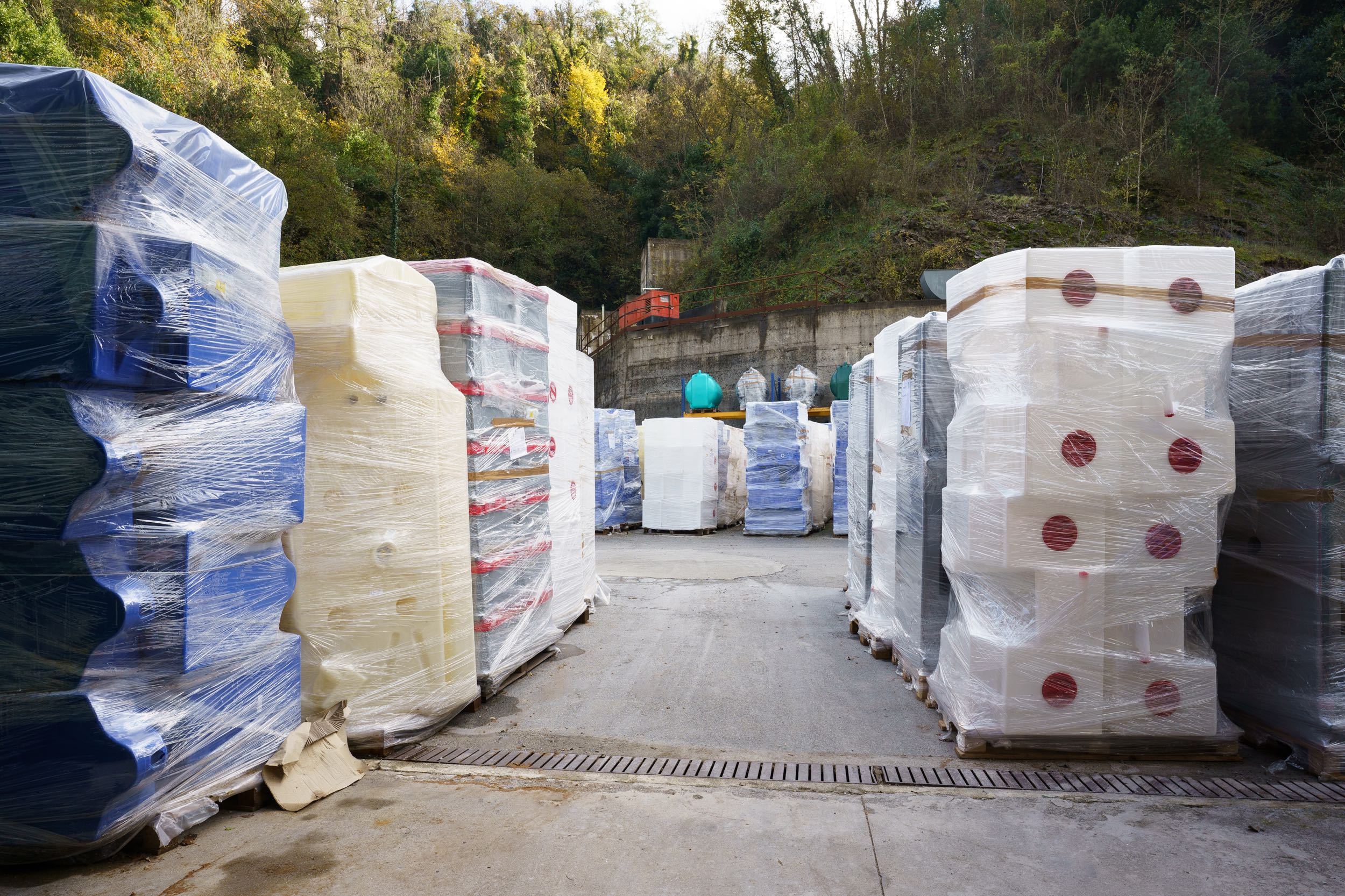
DELIVERY
Where once the packing has been realized with an automatic machine, a delivery note is assigned and moved to the storage area. At this point an employee will carry out a final check of the batch, before being shipped to the customer.
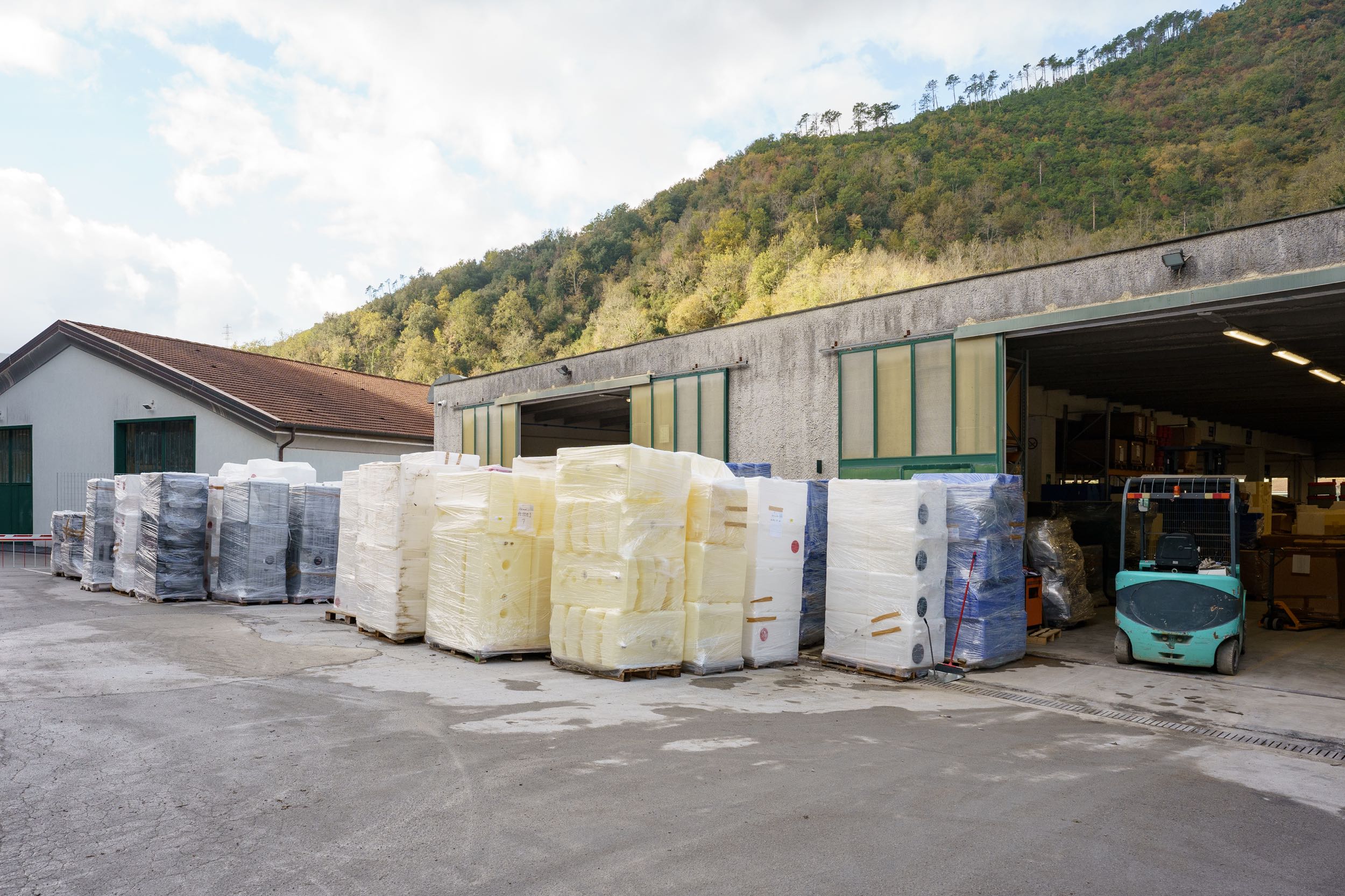